
Do you all know the term "E-Den"? E-Den is the name given to the trains running in the metropolitan area when the national railways were privatized. However, it did not become widely known as many people do not seem to remember it.
There are many things that have been created with great effort but have failed to become popular.
It is difficult to promote manuals, so you may have had experiences like the following.
"I created a manual, but it wasn't really used."
"I struggled a lot with creating manuals that are actually used in practice."
In this article, we will introduce management methods to effectively operate manuals.
We will also explain solutions for cases where operations are not being carried out successfully.
While the content of the manual is important, it is not an exaggeration to say that how it is implemented is also a crucial point. We hope that you can use this article as a reference to assist in the management of manuals used in practice.
- Table of Contents
1. The internal manual is not being utilized! What is the solution?
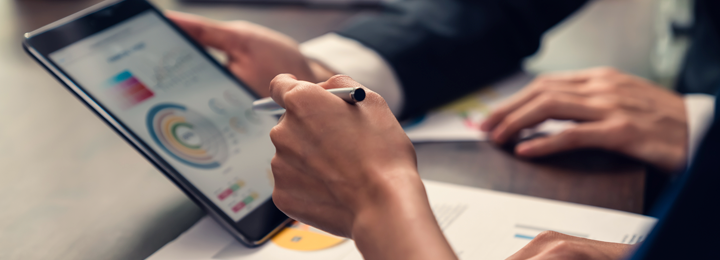
In this chapter, we will introduce methods for effectively utilizing the internal manual, which is the main topic. If you feel that the internal manual is not being utilized, we hope you will read this chapter and find it helpful in resolving the issue.
・How to Effectively Utilize Internal Manuals
The key point is to conduct regular updates. This is because if the content becomes outdated, it can no longer serve its purpose as a manual.
How do you perceive manuals? There are various interpretations, but it is undoubtedly true that they are a "go-to resource in times of trouble."
For example, tasks or jobs that are only performed once a year are often easily forgotten. Are there any tasks that you always make mistakes on? In such cases, manuals should be the reliable resource you can turn to.
"How do I proceed from here? I don't understand, so let's try following the manual."
In this way, the manual exists as a last resort.
But what happens if that manual is not helpful? For example, if the content is not updated and there is a gap between the phenomena occurring in front of you and the manual. Business operations may not run smoothly, which would be problematic. It can be said that it is better to be just problematic than to face worse situations. In the worst case, it could lead to accidents or significant losses.
If it is found that the manual is also unusable, many people will likely direct negative emotions such as disappointment and discouragement towards the manual. If this phenomenon continues, the manual will not be trusted or utilized.
In this way, manuals must be a reliable presence in business. Therefore, it is essential to regularly update the manuals to ensure they are always kept up to date.
・Benefits of Organizing Manuals
Up to this point, we have introduced methods for effectively utilizing internal manuals. Among those who have read this far, have any of you thought this way?
"I know that I need to keep updating and checking the manuals. But I find it hard to get started..."
Therefore, I would like to reintroduce the benefits of organizing manuals. I hope you can recognize these benefits again and take action accordingly.
Benefit 1 of Organizing Manuals: Efficient Business Operations
By organizing the content of the manuals, you can achieve standardization of operations. Standardization of operations leads to stable quality work for everyone. In other words, it is possible to reduce the likelihood of small mistakes and troubles that may occur in the operations.
"I want to do that job, but I have to fix this mistake first..."
Everyone has had experiences like this. As standardization of operations progresses, such unnecessary mistakes will disappear, and operations will run efficiently.
Benefit of Organizing Manuals ②: Reduction of Training Costs
By organizing the content of the manuals, you can reduce costs aimed at immediate effectiveness. As long as the content of the manuals is well-structured, it is entirely possible to bring new employees closer to immediate effectiveness by training them according to the manuals. Of course, manuals alone are not sufficient for effective training of new employees.
However, having a manual eliminates the need for trainers to provide constant supervision. In other words, it can reduce training costs. Additionally, if the manual is well-organized, it will help in understanding the overall operations and serve as a reference for future reviews, thus leading to a reduction in hidden training costs.
・Risks of not maintaining manuals
We have introduced the benefits of maintaining manuals, but conversely, we will introduce the risks of not doing so. By understanding these risks, we hope you will recognize the necessity of maintaining manuals once again.
There are many risks associated with not maintaining manuals, but one of the most representative is that operations do not proceed efficiently. This is because the methods of conducting business are not standardized, leading to time being spent on checks and communication.
For example, let's say that the font for the newly created document is decided to be Meiryo. However, if the manual is not updated, this fact will not be known. What will happen then?
Person A will create the document in Gothic font, while Person B will use MSP Gothic. In this case, the reviewers will need to point this out each time, and it will become necessary to inform everyone.
By not updating the manuals in this way, unnecessary work will occur.
2. What are the key points of manual management to achieve business standardization?
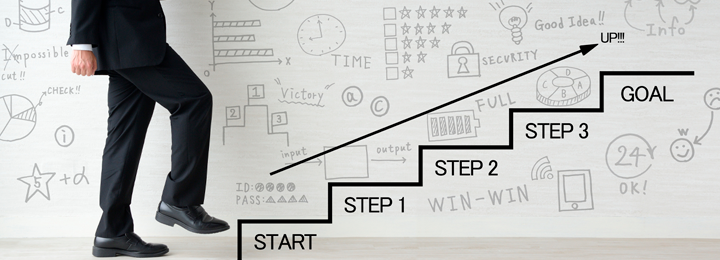
In the previous chapter, we introduced how to effectively utilize internal manuals. In this chapter, we will pick up and introduce three methods for managing manuals to achieve business standardization.
Manual Management Method ①: Quantifying Manual Utilization Status
The first point is to quantify the usage of the manual.
For example, by quantifying usage metrics such as the number of views of manual pages, issues with the manual can be identified.
Of course, simply quantifying the data does not make the issues clear. Extracting the issues will require interviews with the stakeholders, but quantification helps in finding a starting point.
For example, let's say there are pages that are used more frequently in a specific department than in others. Based on this starting point, we will conduct interviews with the responsible parties.
"The fact that it is frequently viewed means that this manual is difficult to understand?"
"Does this department perform the tasks related to the frequently viewed pages more often? Should we provide more detailed descriptions?"
By conducting hearings with the stakeholders in this way, we can identify the issues.
By solving issues through a combination of quantitative and qualitative data, we move closer to a better manual.
Manual Management Method ②: Create a System to Utilize Manuals
The second point is to create a system for utilizing manuals. This is because simply saying to use the manuals makes it difficult for them to be established. Changing people's behavior and thinking is not an easy task.
Therefore, let's make it a rule to refer to the manual. For example, we will always use the manual for training. By having new employees and trainers read through the manual together, we will establish a system to ensure that the manual is always checked.
Manual Management Method ③: Visualizing the Acquisition Status of Knowledge and Skills
The third point is to visualize the acquisition status of knowledge and skills. This is because visualizing it allows us to see whether knowledge and skills have truly been acquired. For example, we will conduct a simple paper test based on the content described in the manual. If you read the manual well, you should be able to answer, so it is possible to understand the level of comprehension through the scores.
In this way, let's quantify the usage of manuals and create a flow for manual utilization, as well as quantify the acquisition of knowledge and skills. This will enable better management of manuals that are more frequently utilized.
3. With Human Science, we can consistently handle everything from business visualization to manual production.
How was it?
This time, we introduced how to effectively utilize manuals. By using manuals effectively, it becomes possible to achieve standardization and efficiency in operations.
I am well aware of the benefits that come from effectively managing manuals, but I think there are many who find it difficult to actually engage in this. Rather, it may be more accurate to say that there are those who want to engage but simply cannot find the time to do so.
While we understand the importance of operating manuals in this way, outsourcing can be one solution for those who are unable to manage it.
Human Science has a proven track record of creating numerous manuals since 1985. We are truly a professional group in the field of business manual creation. If you have any concerns regarding the creation of business manuals, please feel free to consult us.
Feature 1: Extensive manual production experience, primarily with large and global companies
Human Science has a track record of producing 2,854 business manuals for 215 companies, primarily in the manufacturing and IT industries. We have had notable clients such as Microsoft Japan, Cygames, and Mitsubishi Electric.
Feature 2: Research and Analysis by Experienced Consultants - Output
The creation of business manuals is handled by our experienced consultants at Human Science. Our skilled consultants will propose clearer business manuals based on their extensive experience and the materials provided. Additionally, it is possible to create manuals even from the initial stages without any materials. The assigned consultant will conduct interviews and carry out the manual creation.
Feature 3: Not only do we create manuals, but we also provide support for implementation.
Human Science is also responsible for the important phase of "establishment" following manual creation. For example, even after the manual is created, we will conduct updates and hold manual creation seminars. By implementing various measures, we approach the establishment of the manual in the field.